Lagoon Shipyard Belleville, France – 40-46 Feet
Welcome to the Lagoon Shipyard Belleville, France, the bustling hub of Lagoon catamarans ranging from 40 to 46 feet. In this blog, we’ll take you on a journey inside the Lagoon factory and explore the meticulous steps and processes involved in crafting these magnificent boats, from the initial stages of construction to the final touches. Lagoon takes pride in its sustainability efforts, evident in the factory’s certifications and commitment to eco-friendly practices.
Building a 40-46ft Lagoon Catamaran
At the Lagoon factory, the creation of a 40-46ft catamaran involves several crucial steps that ensure precision and quality.
There are tens of thousands of parts necessary to build a Lagoon Catamaran. The process of ordering these parts to make your dream catamaran begins 6 months before anything happens at a factory manufacturing level. By the time the build is ready to begin, everything necessary is in place.
Moulding – Preparation
When you enter the factory’s moulding area, the first thing you see is a team of almost all female staff cutting out each and every piece of fibreglass necessary for the building of your catamaran. There are all sorts of thicknesses, strengths and weaves depending on where the vessel material will be laid. Next to this manufacturing line are vast vats of resins that will bind the moulding process through an infusion system. Once prepared, the cloth and resins are loaded and moved to the moulding area.
Moulding
The process of moulding the hull and deck is intricate and carefully controlled. This is where much of the strength and integrity of your vessel is built in. The first step is the outermost part of the vessel, the Gelcoat – this is sprayed on the prepared moulds to an exact thickness. The next stage is critical and is a wet layup of woven rovings and resin. This is hand rolled and needs to ensure that no air exists between the gel coat and glass fibres. Once these 2 steps have been completed, the team set about preparing the vessel for the infusion. Preparation means the laying of dry woven rovings sandwiching between them, a system of articulating end grain balsa as the core.
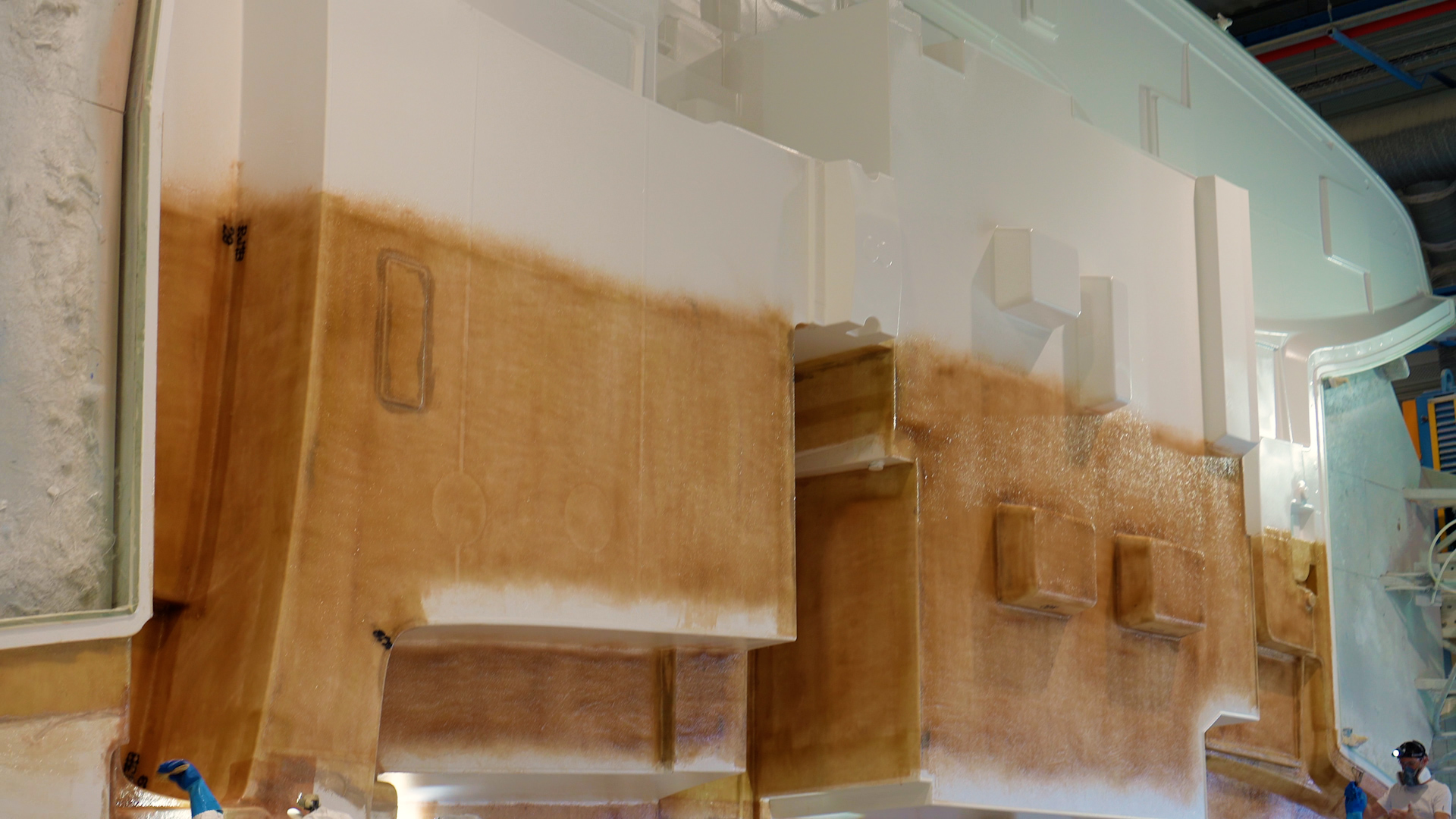
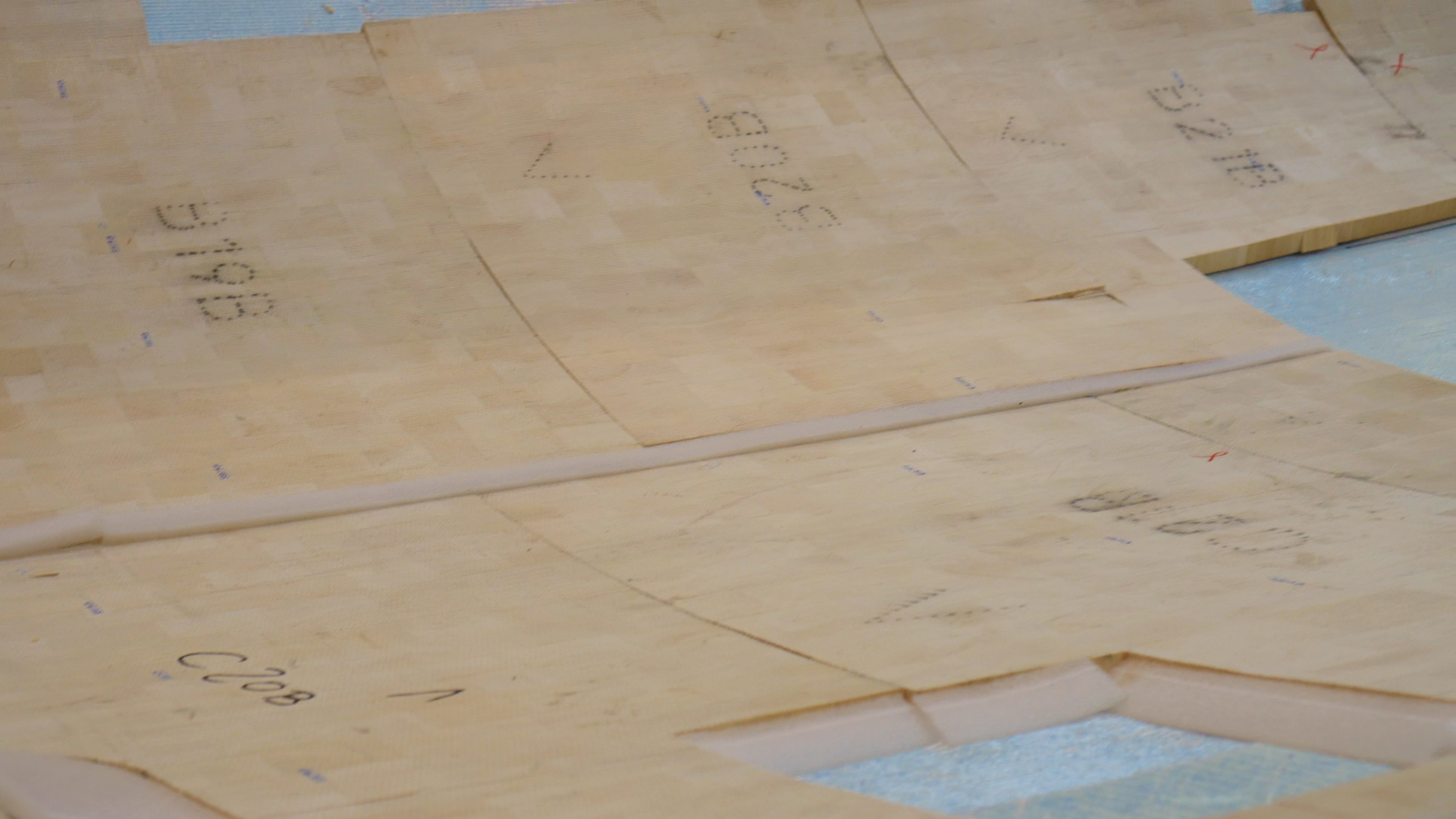
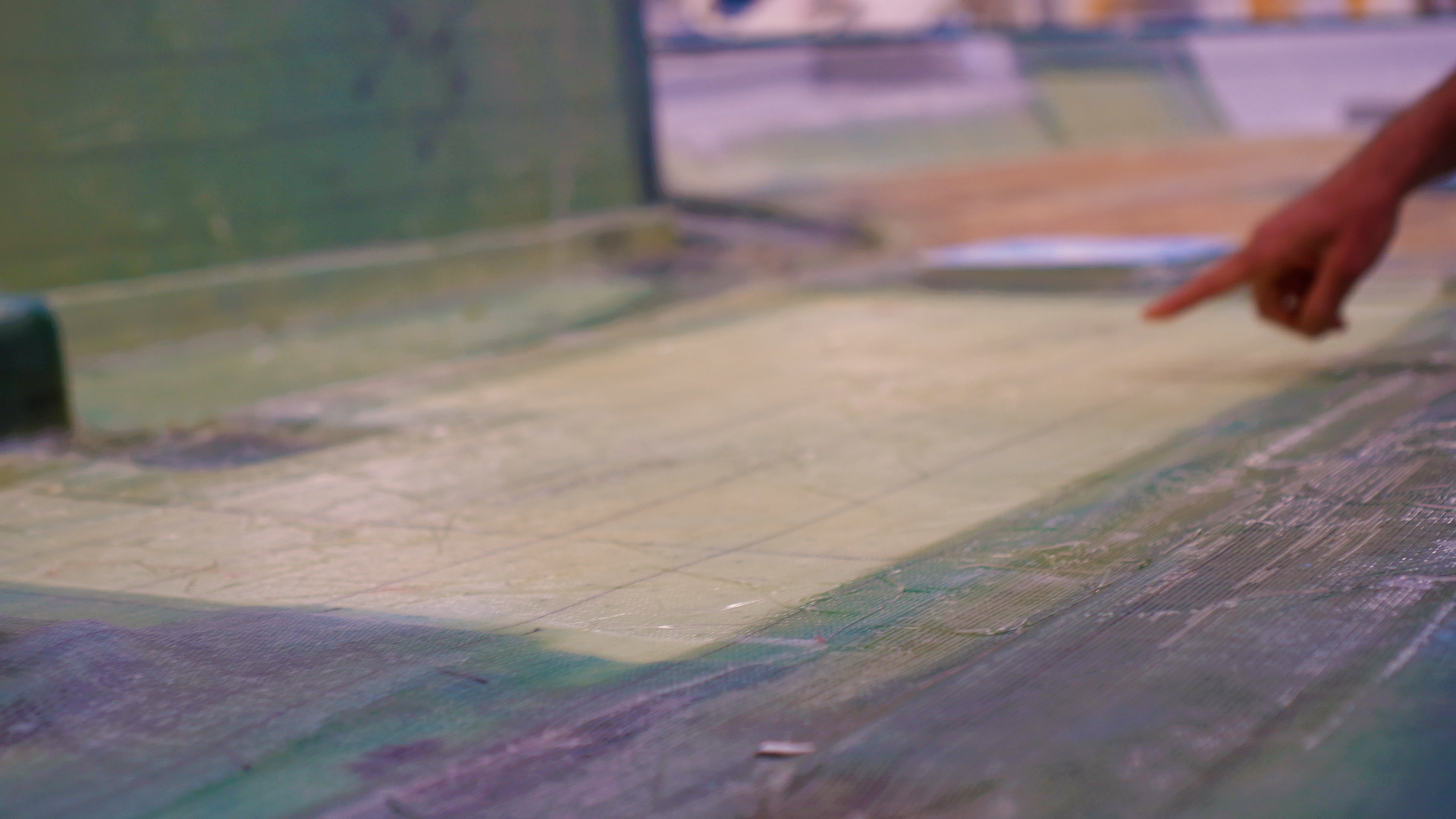
Infusion
The vessel hull and superstructure are infused as one and incorporates the keel. Infusion means covering the moulds in an air-tight bag, sucking out the air to create a vacuum, and then allowing the resin to be “Sucked” through the fibreglass and core until fully saturated. The end grain balsa is in very small individual blocks, which allow each piece to be fully saturated and sealed with the resin. This infusion method is not only a more accurate way of boat building, it is better for the workers as there are much less chemicals released into the factories.
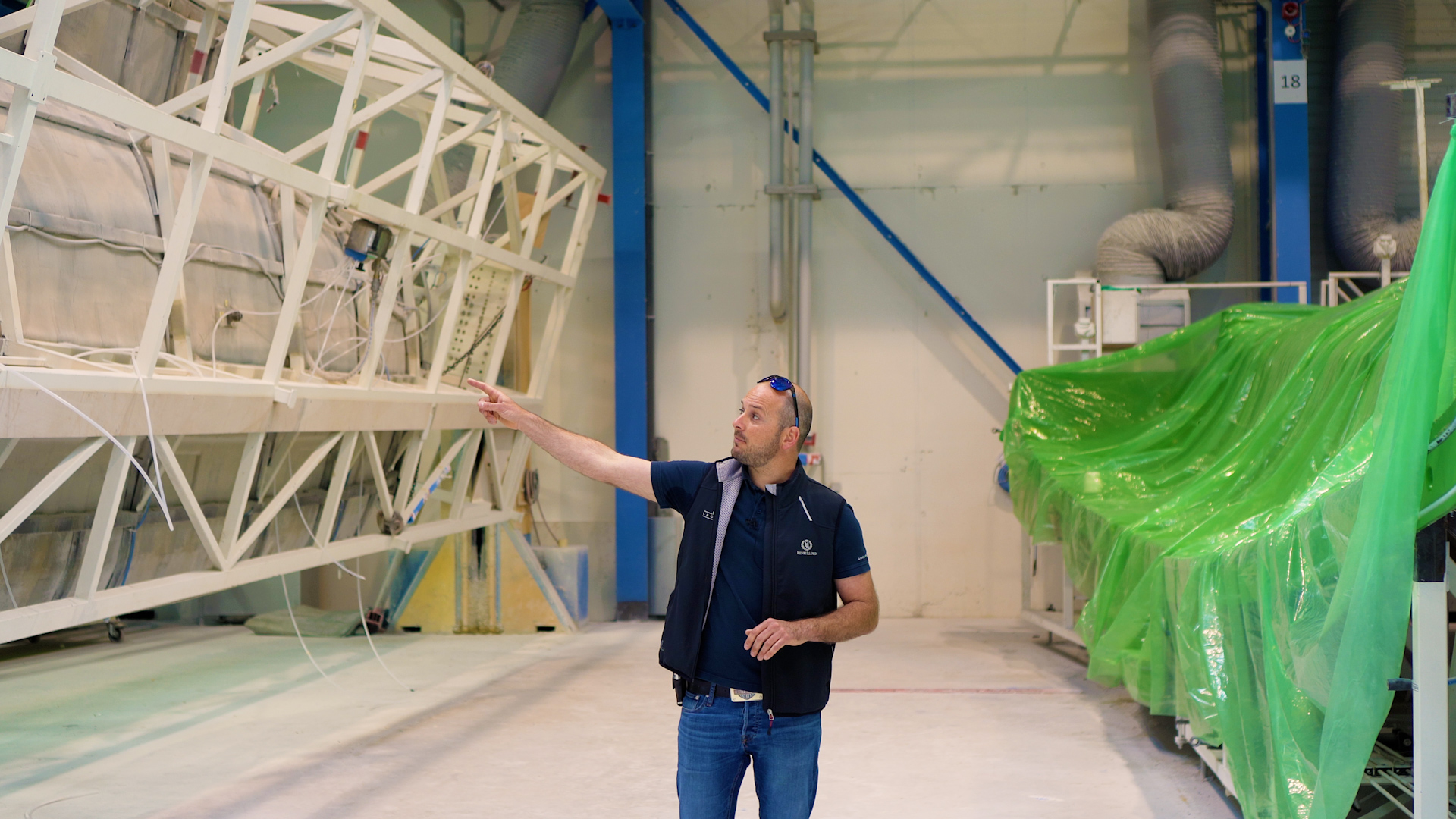
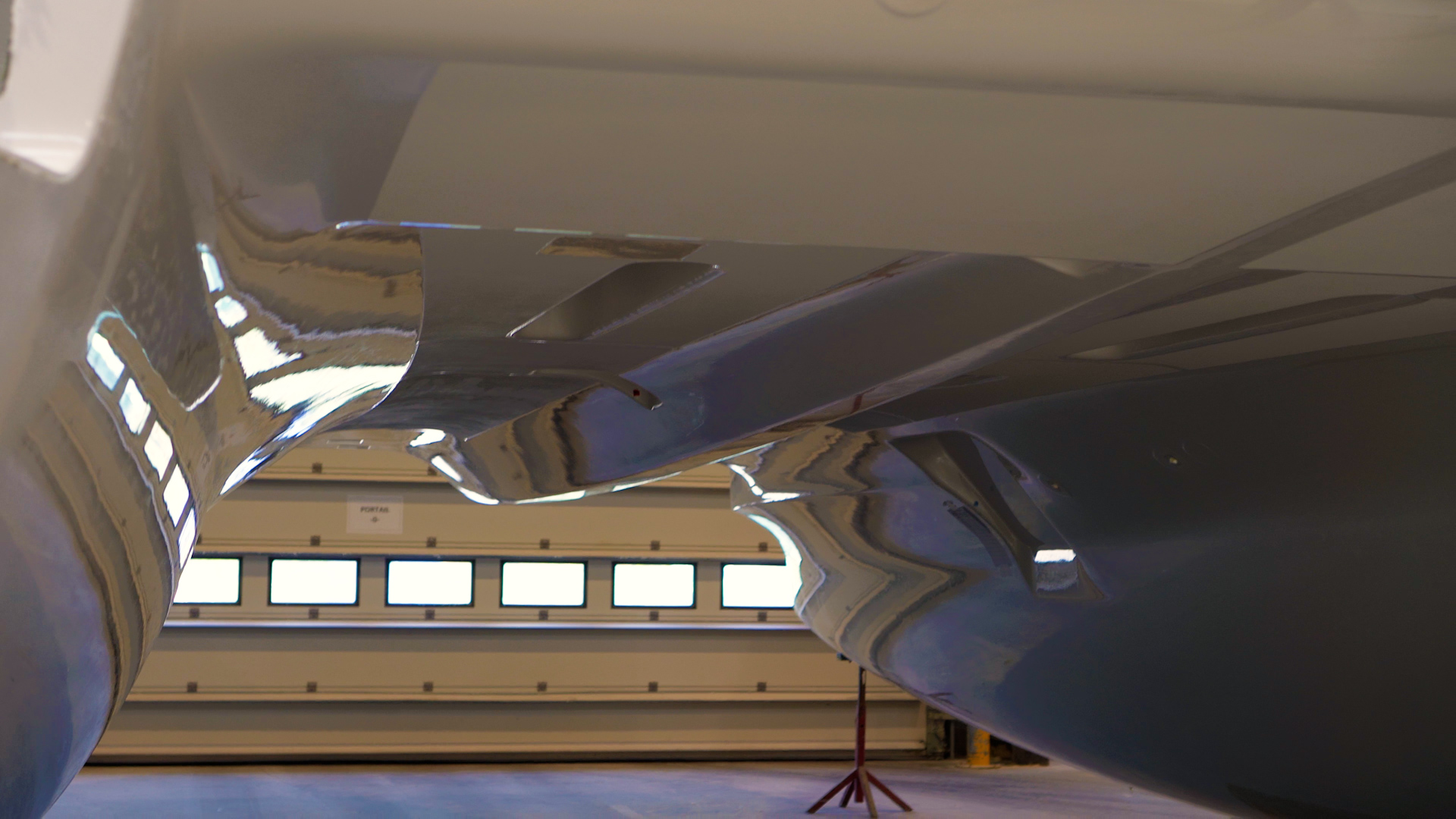
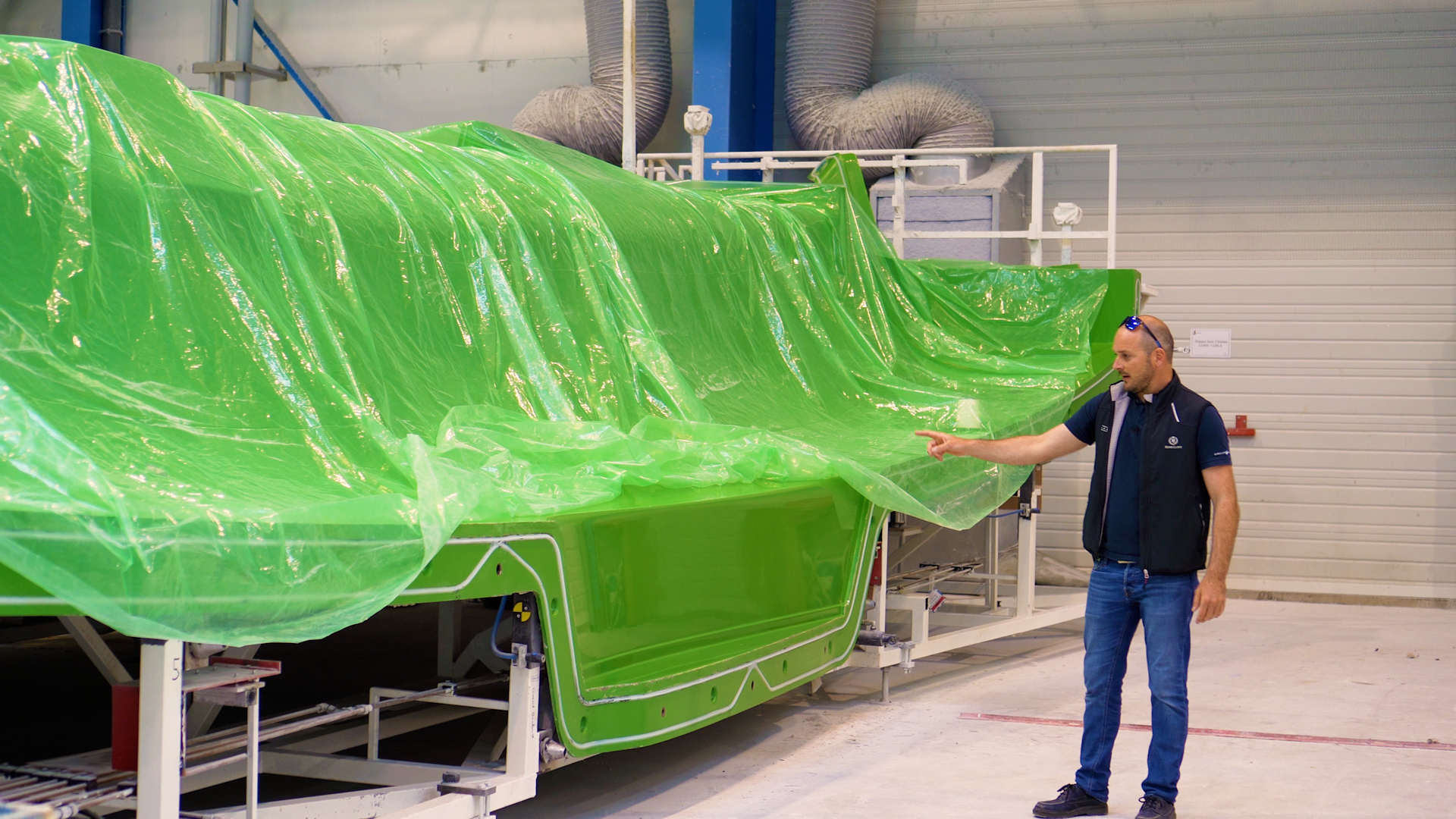
Mould release and finishing
Once the moulding process is complete, the hull and deck are released and moved to a finishing factory where any imperfections are removed using diamond-cutting tools and the vessel is polished and ready for the assembly stage.
Assembly Line
The most impressive and highly organised part of the build process can be found on the assembly line. There are 3 areas running concurrently and moving down the lines with military precision. The hulls are fitted out with all of the running equipment, including engines, plumbing, electrics, airconditioning, generators etc. Down the centre of the hall the interior joinery is prepared and at the same time, the deck is moving down the hall on the far side. Once the interior furniture is fitted, the hull meets the deck, and the marriage takes place!
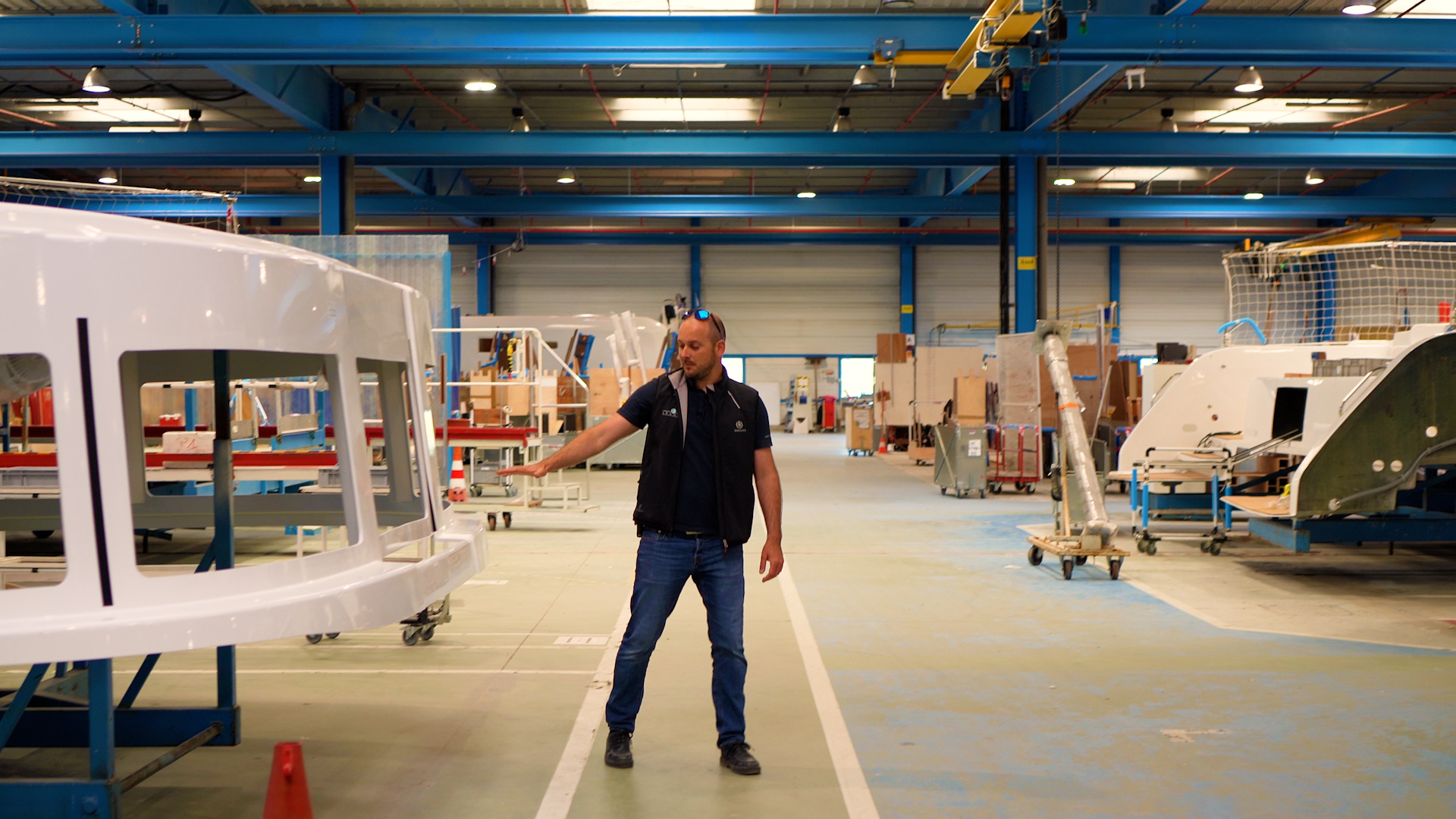
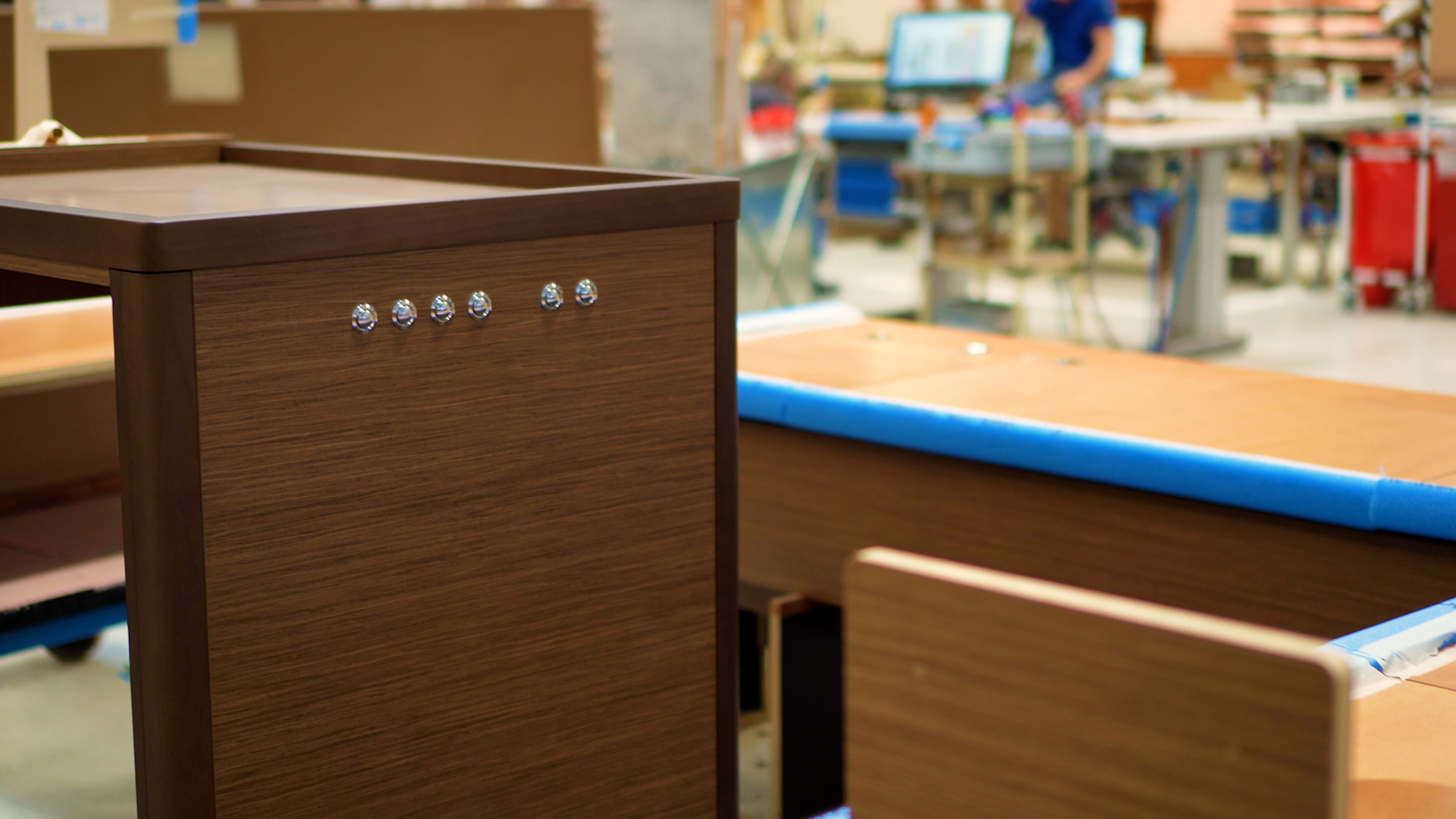
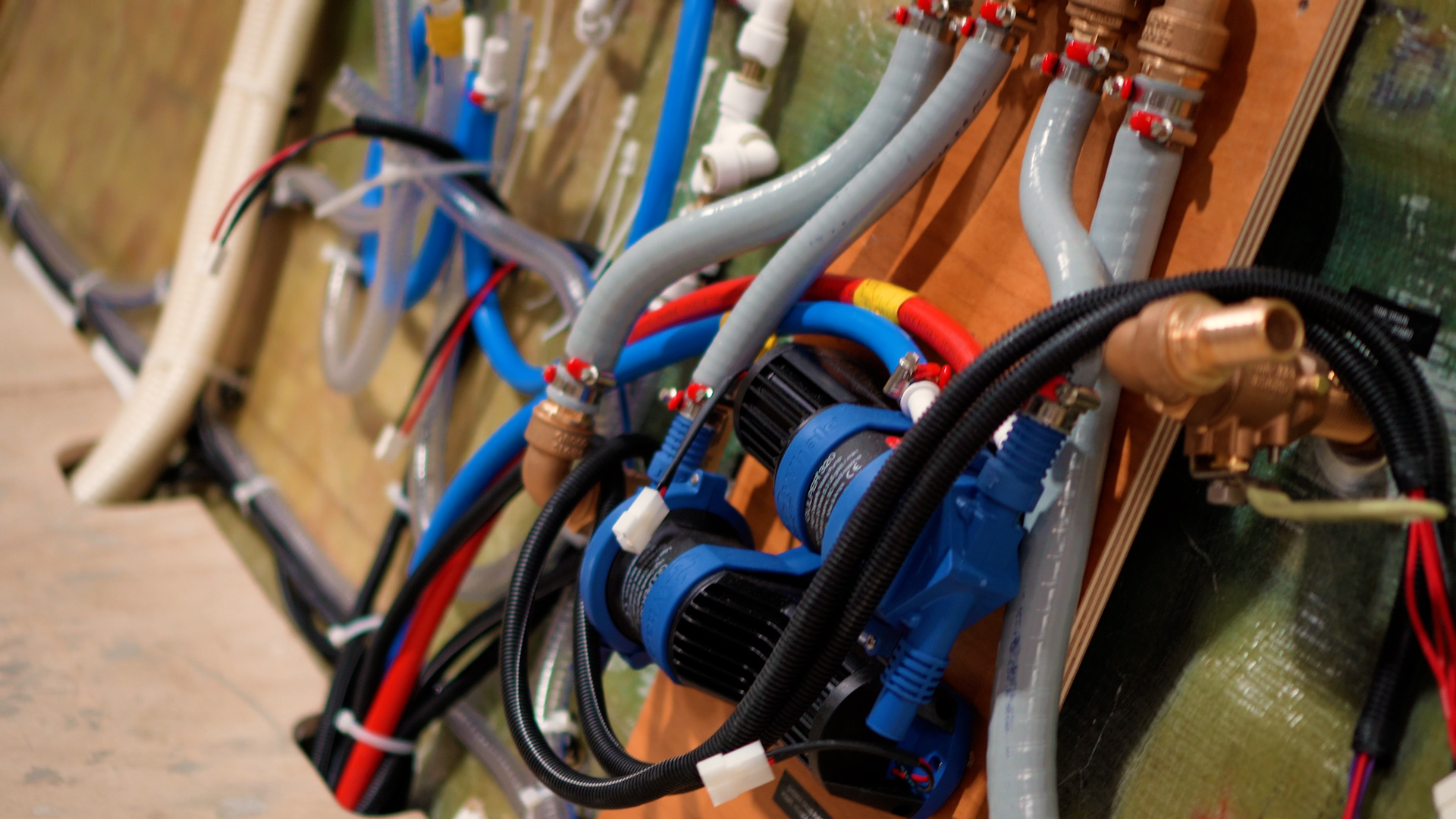
Quality Control
From the very start, and at every stage as the vessel moves through production, there are checks to ensure the quality is always being monitored and, where necessary improved. In effect, everytime the boat moves to a different stage, the workers handing it over treat the next set of workers as their clients. They need to be handing over a flawless product. If this is not the case, the deficiencies are reported back, and improvements are implemented immediately.
Final Steps
Once the boat is together and complete, it moves as one to the huge indoor swimming pool. Here all of the water tests take place, including checking for water tightness and that all systems, including engines, generators, and air conditioning, are functioning as they should.
Once the boat is complete, it goes into the park to await trucking to the dock in Les Sables d’Olonne for final commissioning or to the port for shipping back to Australia.

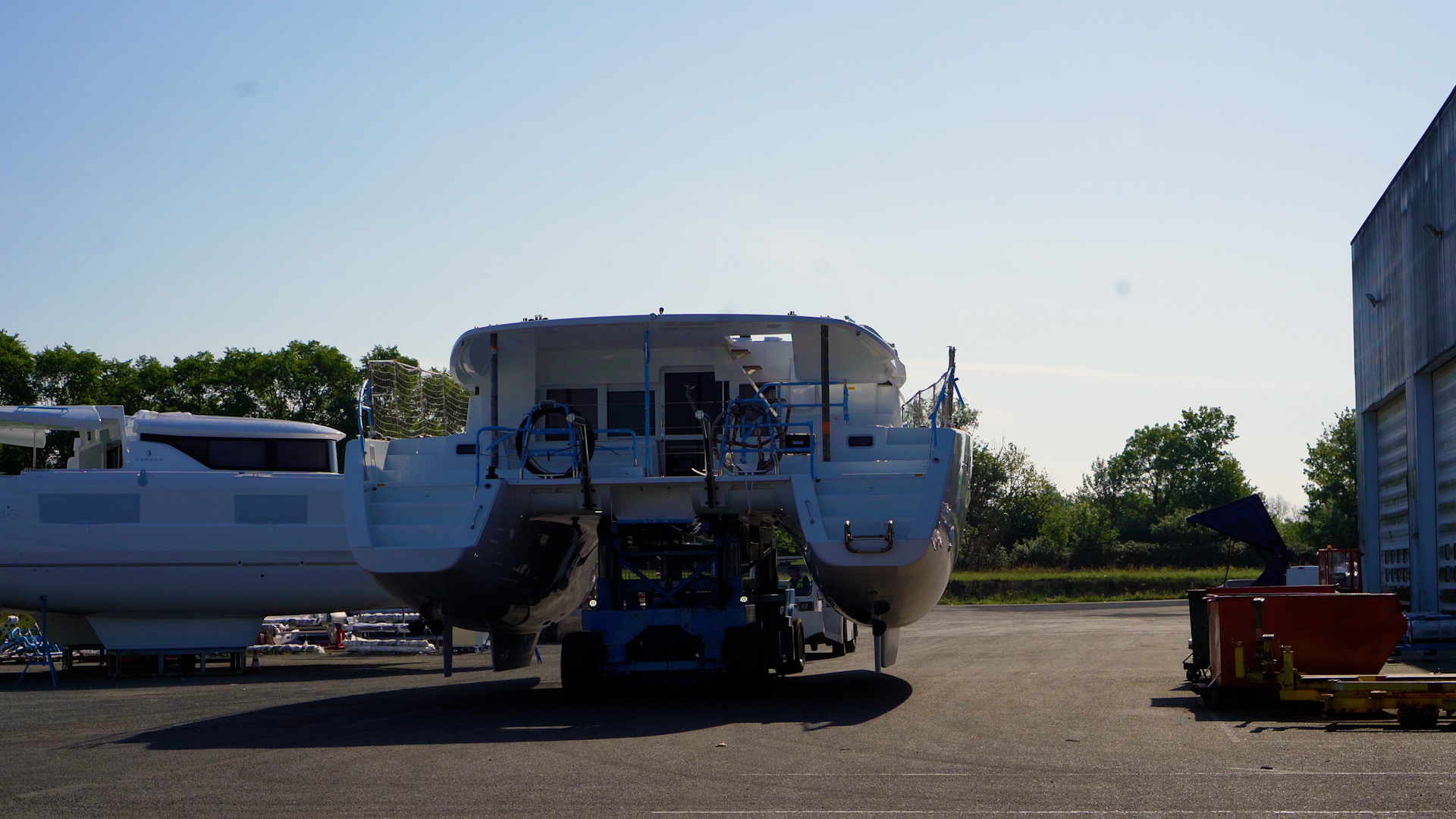
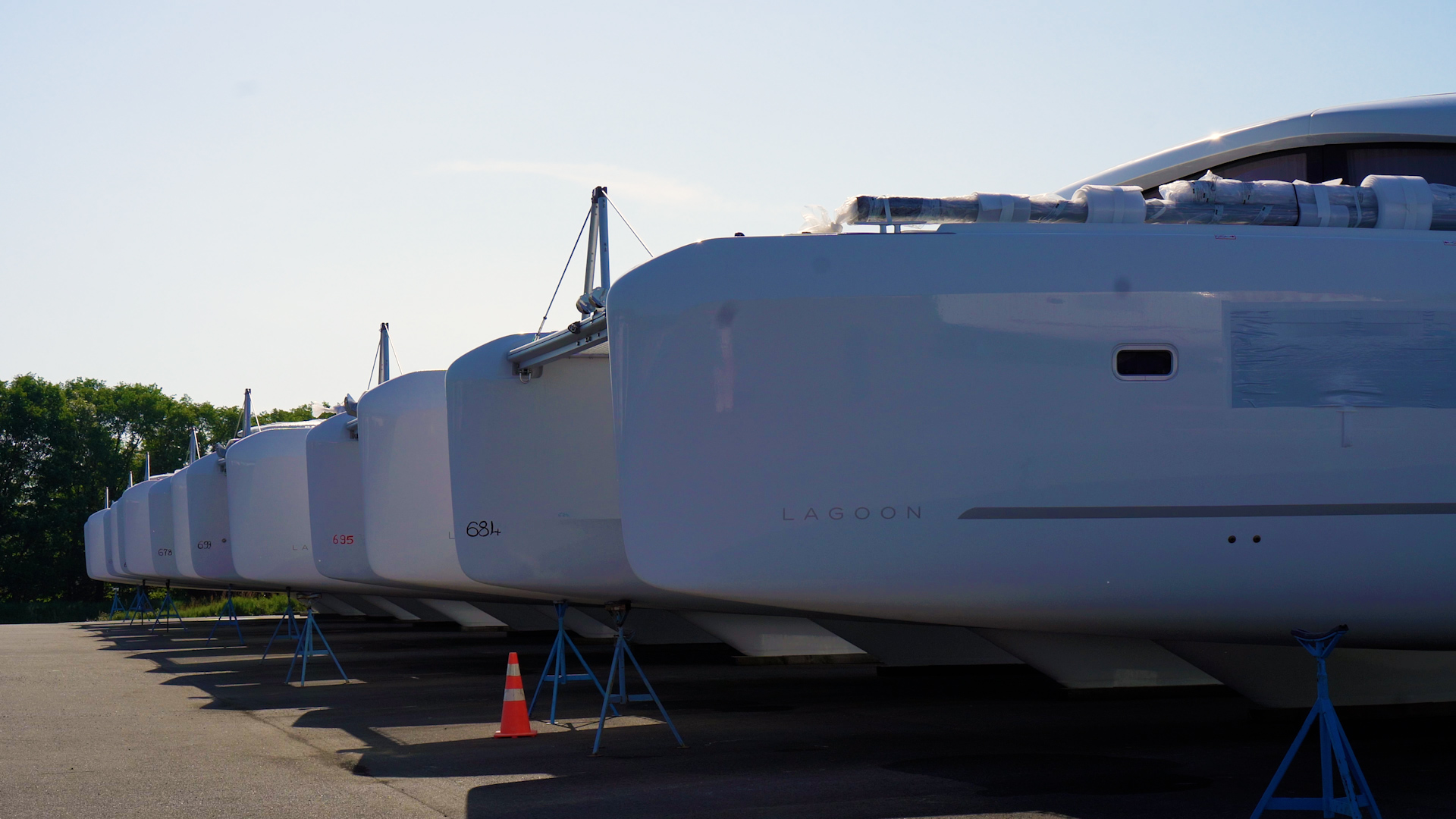
Lagoon’s Sustainability Steps and Certifications
Lagoon is committed to sustainability and environmental responsibility. The Belleville Factory, has received ISO certifications:
- ISO 9001 for quality processes
- ISO 14001 for environmental processes
- ISO 50001 for energy management processes.
These certifications showcase Lagoon’s dedication to maintaining high standards in their production methods.
In addition to certifications, Lagoon is actively using more eco-sourced materials in their boat construction. These include hemp fibre, bio-resin, and wood from FSC-certified forests. The company also prioritises using recycled fabrics, further reducing their environmental footprint.
A Bright Future for Lagoon Catamarans
As you walk around the factory, the passion and dedication of around 400 staff members is clear. Nearly half of the workforce comprises women, making it a progressive and inclusive workplace.
We hope you enjoyed this glimpse into the Lagoon factory and their dedication to crafting remarkable catamarans while embracing environmentally friendly practices. For any further information or inquiries about Lagoon and their catamarans, don’t hesitate to reach out to the team at TMG.
LATEST FROM THE LAGOON CATAMARAN BLOG
Catamaran Sailing with A Family of Four
Meet Jasmine and Owen Richards—a couple who traded suburban life for a floating home. Alongside their two young daughters, Indy and Luca, they’re living full-time aboard a Lagoon 450 catamaran, embracing a new rhythm of life, education, and adventure...
Master Catamaran Sailing with Lagoon Campus
Launching in 2025, TMG Yachts introduces the Lagoon Campus—a tailored training program designed to upskill future Lagoon catamaran owners....
Everything You Need to Know About the Lagoon 38 Catamaran
The Lagoon 38 catamaran is the latest addition to the Lagoon range, launching in 2025. With modern design, increased volume, and smart sailing features, it offers big-boat comfort in a compact size. Discover everything you need to know about this exc...